For those of you who haven’t heard of it yet, rotational moulding is a quite awesome manufacturing technology, perfect for producing robust, durable plastic products of any size.
Thanks to their solidity and waterproofness and because of their environmental benefits, rotomolded products are perfect for the wastewater treatment sector.
When designing an innovative product, it all comes down to selecting the right processes so that your product can do its job well, without compromising on durability or performance.
Here’s 3 reasons why rotational moulding seemed like an obvious answer to us.
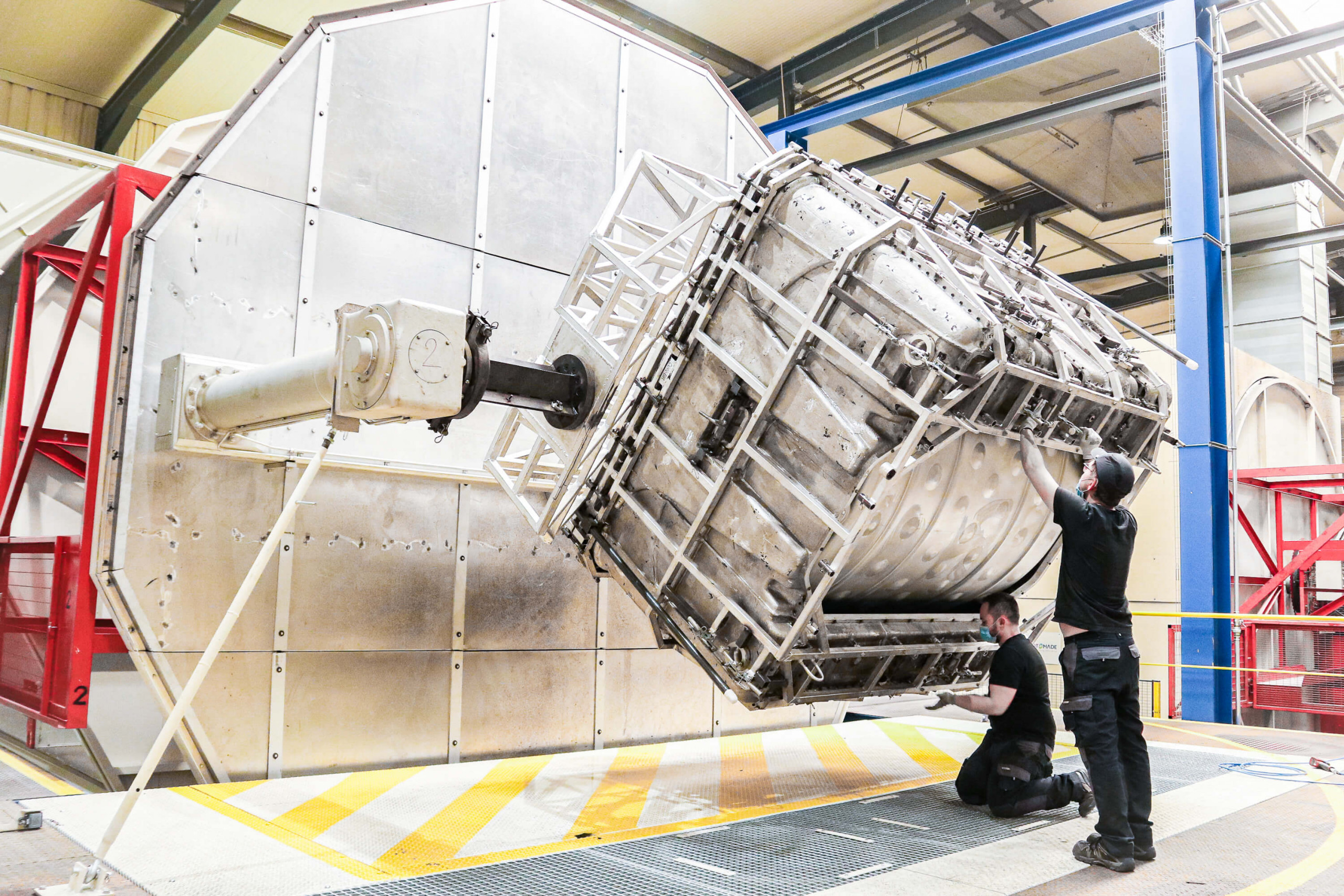
1 – Rotational moulding offers the highest quality plastic pieces, that are durable and resistant to corrosion
Rotational moulding is the perfect manufacturing technology when developing durable wastewater treatment plants. The manufacturing process is not only efficient, using the highest quality, corrosion resistant, and recyclable materials (HDPE), but this process also guarantees our tanks will be 100% robust, with consistent, higher thickness walls and no weak points that can cause stress on installation or degradation over time due to cracks (even at corners or edges!).
This means that any plastic piece made using rotational moulding is less likely to break, corrode, or collapse over time.
Rotational moulding also produces precision cut-outs for access points and utility connections that allow installers to easily connect pipes. The result is a highly durable project that can be used reliably year after year without needing repairs – unlike other types of plastic or metal products where leaks need constant attention and maintenance.
2 – It allows the wastewater treatment plant installation to be much easier, especially in remote locations.
One of the benefits of the BIOROTOR wastewater treatment plants lies in their cutting-edge design, made thanks to rotational moulding.
We wanted to create an all-in-one wastewater treatment plant, that would be quick and easy to install, without spending days on building concrete tanks. Our BIOROTOR units come pre-assembled and ready to install, which means that all you have to do is pop the BIOROTOR in its spot, do the proper electrical and piping installations and turn on the water! Plus, the high thickness of the tank’s walls allows for both above-ground installations as well as below ground implementations.
And guess what… We designed our BIOROTOR tanks to be a standard size so they can fit perfectly in a container and lower shipment costs (and footprint!)Why Choose BIOROTOR?.
3 – Rotational Moulding is a green technology that uses less energy and creates less pollution
Rotational moulding is a cleaner manufacturing process.
We only use the safest cleaning and maintenance methods –with water-based solvents– because our company isn’t just about treating wastewater, it’s also about producing responsibly. We have a responsibility to avoid adding harmful chemicals to drinking water supplies and chemical vapours to the air we breathe.
Rotational moulding is a relatively low-energy and eco-friendly manufacturing method because the process consumes less energy than any other plastic manufacturing technology.
We even went so far as to re-use the heat generated by our XXL ovens to power our heating system in wintertime… Clever, right?
One last ecological benefit of rotational moulding is that these plastics are made from 100% recyclable materials, so once the plant reaches its lifespan It can be shredded into scraps that will be recycled back into new products without worrying about waste accumulation issues.
4 – (bonus) Rotational moulding is fascinating
Yes, we know… This might not be a very “valid” reason… But, have you ever watched a large rotomoulding machine in action? It’s so captivating!
It looks like a tiny roller coaster, spinning in every direction. The machines are so fascinating, we could watch them going on and on and on… Anyone with a love for machines –like BIOROTOR’s founders, Antoine and Gerrit—will love watching the process!
Watch the short video above of a BIOROTOR tank being manufactured and you’ll understand how hypnotic this manufacturing technology can be.
CONCLUSION
The BIOROTOR wastewater treatment plant tank is a good example of why rotational moulding has become so popular. This manufacturing process allows us to produce high-quality products made of 100% recyclable materials, with multiple additional benefits like easy installation in remote locations, or an eco-friendly process that’s better for the environment. When it comes to green technologies- there’s no better choice than one using less energy and creating less pollution!
At BIOROTOR, we know that you need durable systems to withstand the challenging conditions of your industry. If you want to learn more about all the benefits of our innovative wastewater treatment plant, just send us an email at info@biorotor.com ; a quick chat with one of our expert Liz and you’ll understand what makes BIOROTOR the best choice for your sewage system.